Two types of objectives can be distinguished leading to two different tests.
- The burn-in test, designed to detect and reject as quickly as possible any transducers which are statistically faulty in the very first period of their life (early failures)
- The ageing test through which the stability of the transducer’s performance over time is described.
These two tests are undertaken for a given level of acoustic power with excitation cycles fixed according to the application, usually a sequence of excitation periods (ON) and rest
periods (OFF). The length of time ON and the ON/OFF duty cycle at a given power level are the determining parameters of use to evaluate the transducer’s performance.
Burning tests
The solicitation level of the burn-in test is set at a level that is greater than or equal to the maximum power level provided for in the application. The test duration should also be significant for the application. During the excitation cycles, the heating of the transducer is controlled. This measurement can be taken using thermocouples implanted in the transducer. A temperature alert is programmed beyond a threshold fixed according to the application and the technology of the characterized transducer.
Example of a burn-in test of 15 min at 20 Wac/cm², with cycles of 10s ON/10s OFF, for a transducer operating at 900 kHz; the heating of the transducer is measured by thermocouples at eight points. In this example, it reaches the maximum value of 20.5 °C.
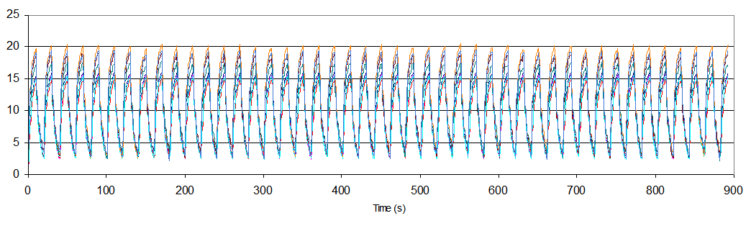
Heating inside the active part of the transducer (8 locations) recorded during 15 min of (10s ON / 10s OFF) excitation cycles
Ageing tests
For longer durations, of around the anticipated lifetime for the type of transducer under consideration, an ageing test can be undertaken according to conditions defined on a case by case basis by IMASONIC and the customer. During these tests, in addition to the temperature of the transducer, continuous measurement is taken of the electric power transmitted and reflected, the efficiency, and the electric impedance, which proves to be a good criterion for detecting a transducer malfunction.
The following curves represent the evolution of the efficiency, temperature and electric impedance of a transducer operating at 900 kHz, tested at 23 Wac/cm², with cycles of 10 ON / 10 OFF during 400 hours. The measurement uncertainties are represented by the dotted curves:
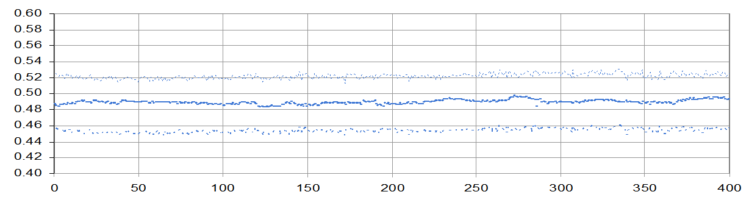
Transducer efficency (%) recorded during the ageing test of 400h
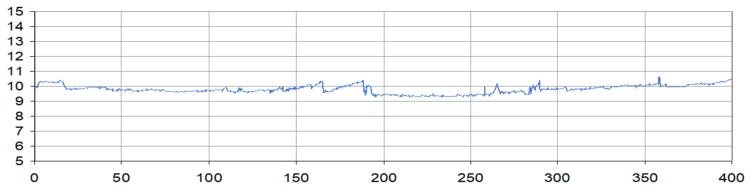
Transducer heating (°C)
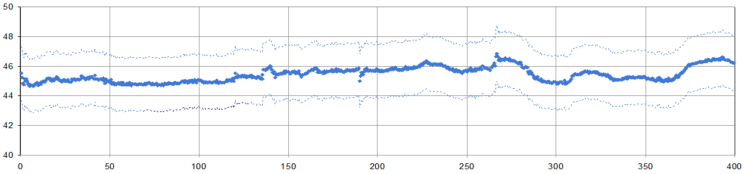
Real part of the impedance (ohms)
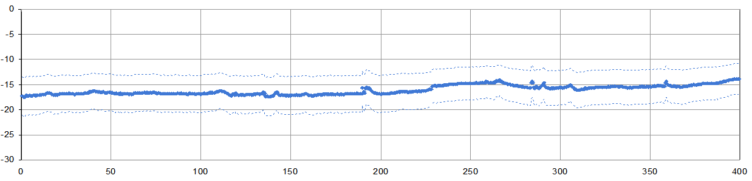
Imaginary part of the impedance (Ohms)